advertisement
The Human Cost Of Technology In Manufacturing
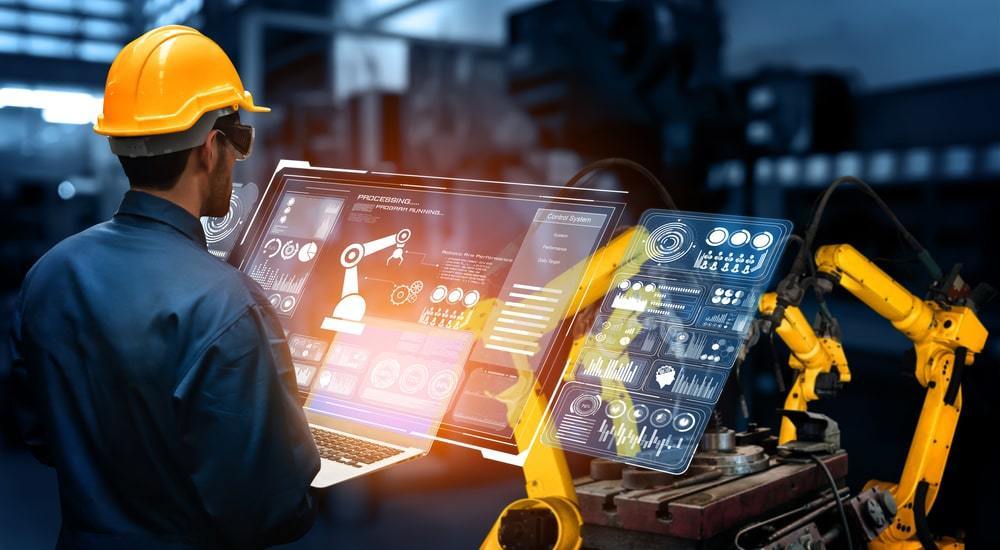
Let’s start off by looking at some spectacular examples.
- The BMW Group uses automated image recognition for quality checks and inspections with an AI application that compares the vehicle specifications data with a live image of the vehicle from the assembly line. This algorithm identifies deviations from standard specifications in real time.
- PepsiCo has adopted Microsoft’s Project Bonsai. Why? To improve the quality of its popular snack, Cheetos. The final perfect product depends on several things from water ratio to cutting speed. Project Bonsai works by applying a computer vision system. This, in turn, uses incoming data to make adjustments when the product falls out of spec.
- Canon’s asset defect recognition system combines human expertise with AI. The machine learning-based Assisted Defect Recognition technology system analyses images of inspected parts which processes and identifies defects the human eye misses.
- Schneider Electric’s predictive IoT analytics solution improves safety and cuts costs while helping enterprises meet their sustainability goals. The tool is based on Microsoft Azure Machine Learning service and Azure IoT Edge that assists shop floor operators in building models. It has increased efficiency by 10 per cent to 20 per cent.
What do all these success stories have in common? The collaboration of humans and technology is what.
The human cost of technology in manufacturing is a narrative that demands attention – a story of both triumphs and challenges. One where the intersection of innovation and its impact on workers reveals a multifaceted tale of empowerment and displacement, growth, and concern. With the smart industry moving towards an increasingly digital age, we have to unravel the intricate threads that bind technology and its consequences in a bid to shed light on the experiences of those whose lives are intricately woven into the fabric of modern manufacturing.
advertisement
The rapid advancement of technology in manufacturing has undoubtedly brought numerous benefits, including increased productivity, improved efficiency, and the ability to produce complex products at scale. However, it has also come with a human cost that deserves careful consideration. The human cost of technology in manufacturing refers to the impact that automation, robotics, and other technological innovations have on workers, their jobs, livelihoods, and overall well-being.
Several key aspects contribute to the human cost:
- Job Displacement And Unemployment:
As automation and AI technologies are integrated into manufacturing processes, certain tasks previously performed by humans may become obsolete. This can lead to job displacement and, in some cases, job loss for workers who find themselves replaced by machines. While new jobs may be created in emerging technology-related roles, the transition can be challenging for some workers who may face unemployment or need to acquire new skills to remain employable.
advertisement
However, companies ought to judiciously determine what processes warrant automation and what should remain within the purview of human intervention. Kenneth Ogwang’, Head of Digital and Technology – Eastern and Southern Africa at Diageo opines that achieving complete automation should not an objective for companies in the African manufacturing space given the lower cost of human labour compared to other continents.
“This consideration holds weight given the context of operating in Africa, where human labour comes at a price point significantly more affordable when compared to Europe and America. Therefore, it’s advisable to fully leverage human labour and selectively implement automation in areas constrained by the limitations of human effort. Automation should also be pursued when aiming to enhance aspects such as efficiency, productivity, and speed, areas where human labour might fall short,” he says.
- Economic Inequality And Job Polarisation:
The adoption of technology in manufacturing may exacerbate economic inequality by affecting different segments of the workforce differently. High-skill workers who are involved in designing, implementing, and maintaining automated systems often benefit from increased productivity and demand for their specialised skills, leading to higher wages and job security. On the other hand, low-skill, and routine jobs, which are more susceptible to automation, might experience reduced demand, leading to wage stagnation and even job loss for those workers.
advertisement
Additionally, automation contributes to job polarisation, a phenomenon where employment opportunities shift towards the two ends of the skills spectrum – high-skilled and low-skilled jobs – while middle-skilled jobs face a decline. High-skilled jobs involve tasks that require creativity, problem-solving, and complex decision-making, while low-skilled jobs encompass manual and routine tasks that are harder to automate. However, middle-skilled jobs that involve repetitive and routine activities, such as data entry or administrative tasks, are more vulnerable to automation, leading to a reduction in their availability.
- Skills Gap And Training Needs:
The adoption of advanced technologies often requires a highly skilled workforce to operate and maintain them. However, there can be a skills gap between the existing workforce and the new demands of technology-driven manufacturing. Companies and governments must invest in training and upskilling programs to ensure workers can adapt to the changing technological landscape and remain competitive in the job market. Ogwang’, who has more than 17 years of experience working for multinational companies, says organisations need to have a comprehensive strategy-wide training programme that provides employees with internal and external opportunities to gain proficiency in new technologies.
“The work environment should facilitate employees’ upskilling efforts even beyond the workplace, without facing penalties. Additionally, within the organization, the presence of a training policy that empowers employees to pursue training externally is essential,” he says.
- Job Monotony And Loss Of Job Satisfaction:
Automated processes can lead to repetitive and monotonous tasks for workers who may have previously had a more varied and engaging job. This can result in a loss of job satisfaction and motivation, impacting overall well-being and work performance.
If you ever find yourself grappling with the challenges of job monotony, it’s advisable to consider venturing into new areas and seizing emerging opportunities. This involves not only embracing newfound skills but also adapting to the innovative capabilities that accompany new technologies.
Ogwang’ argues that issues of loss of job satisfaction may originate from resisting change. He says employees should adopt a mindset that readily welcomes change when it arises. “Those who resist change are the ones most vulnerable to being left behind by the swift technological advancements. Employees who possess a positive outlook are the ones who manage to adapt and reskill themselves effectively, ensuring alignment with the evolving ways of working”.
- Psychological Impact And Job Insecurity:
The fear of job loss due to automation can create significant stress and anxiety among workers, leading to decreased morale and productivity. The uncertainty surrounding job security in an era of rapid technological change can have detrimental effects on mental health.
- Worker Safety And Well-Being:
While automation can reduce some physical risks associated with manufacturing tasks, it may introduce new safety concerns related to working with robots and advanced machinery. Ensuring worker safety in the presence of automation requires robust safety protocols, employee training, and ongoing monitoring.
Addressing the Human Cost:
To mitigate the human cost of technology in manufacturing, a comprehensive and thoughtful approach is essential.
- Investing in skills development: Offering training and upskilling opportunities to workers to enable them to embrace technology and transition into new roles.
- Creating supportive work environments: Fostering a culture that values workers and prioritises their well-being, including psychological support for job transitions.
- Curiosity and exploration: Employees should begin exploring their surroundings and questioning what other valuable contributions they can make. They should internalise the insights derived from reports and liberate themselves to direct their attention towards other facets of the business.
- Responsible automation implementation: Ensuring that automation is used responsibly and ethically, with consideration for its impact on workers and society. “In instances where it’s logical, automation should be embraced, while also recognizing the value of maintaining human involvement where feasible. Certain facets, like supervision, may not necessarily demand automation, especially when viewed from the African perspective,” Ogwang’ says.
- Social safety nets: Establishing social safety nets to support workers affected by automation, aiding in reskilling, reemployment, and financial security.
The human cost of technology in manufacturing requires a holistic approach that balances technological progress with the well-being of workers. By investing in the workforce’s adaptability, safety, and support, society can harness the benefits of technology while minimising its negative impact on individuals and communities.
This article was first published in the August 2023 issue of CIO Africa magazine.
Thank you sharing the wonderful article, enjoyed lot while reading the post.