advertisement
Tomorrow’s Industries Are Calling
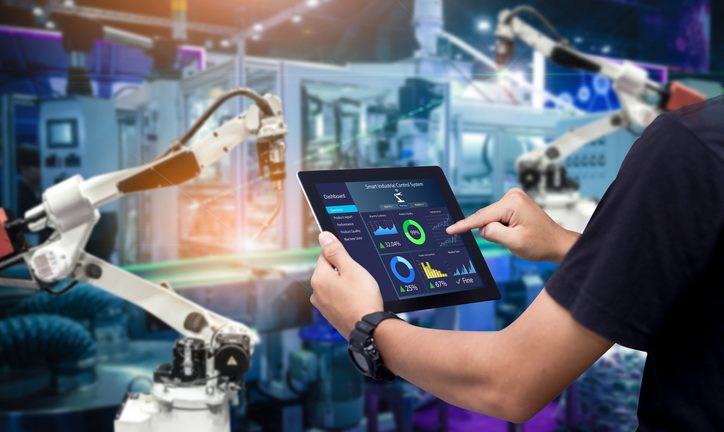
Times have changed, that’s without a doubt. Today, industries thrive on automation leveraging modern technologies to optimise production.
Industry automation describes a wide range of technologies as elaborated by Carol Koech, the Country President, East Africa at Schneider during the second I4R summit for Africa.
She noted that that automation reduces human intervention in processes by predetermining decision criteria, subprocess relationships, and related actions, embodying those predeterminations in machines adding that it uses control systems such as robots, and information technologies for handling different processes and machinery in an industry to replace a human being. It makes manufacturing eco-friendly.
advertisement
“Tomorrow’s industries are calling, let’s make manufacturing eco-efficient, agile and resilient through open automation,” said Koech adding, “Whatever you make, let Schneider Electric help you make it for life by getting ready for universal automation.”
This automation is powered by next-generation technology, centered on the rapid growth of products -tailored to suit consumers – as well as the manufacturing fabrication of those products.
“This is the age of the ‘Industrial Automation’. To be successful in it, companies will need to change the way they do business in the future,” she added. “The gains from building and operating a smart facility goes beyond the production of goods. They embrace planning, supply-chain logistics, workforce, and all aspects of product development and innovation.”
advertisement
Businesses that fail to adopt smart manufacturing technologies and practices risk being left behind, which is why we are seeing a growing number of factories worldwide that exemplify the advantages of smart manufacturing.
Manufacturing systems are already harnessing a full array of new and emerging technologies. The internet acts as the foundation, linking equipment, sensors, analytical tools, and people in ever more intricate and resourceful ways. Big data, robotics, machine learning, artificial intelligence, augmented reality, 3D printing, predictive analytics, all these things and more are now converging. And with the heightened level of control and oversight that they bring, we can now build a “digital twin” of an entire manufacturing system, and so optimise business performance by creating a real-time profile of a physical object or process
The National Institute of Standards and Technology (NIST) defines this new landscape as “fully-integrated, collaborative manufacturing systems that respond in real-time to meet changing demands and conditions in the factory, in the supply network, and customer needs.” Converging and connecting is another way of saying more integrated and more collaborative. This is where manufacturing benefits form a multiplier effect, as operating and information technologies grow stronger in combination, improving efficiency at all levels.
advertisement
The World Economic Forum has highlighted nine of the world’s smartest factories, designating them “lighthouses” that illuminate the benefits of the fourth industrial revolution. That means they have comprehensively deployed smart technologies while maintaining people and sustainability as the heart of their operation. Among these lighthouses is Schneider Electric’s Le Vaudreuil facility in France.