advertisement
Synkron International Putting Engineering Sector On Digital Map
The term digital transformation has gathered a lot of steam recently. Ever since the pandemic, change has been a constant…
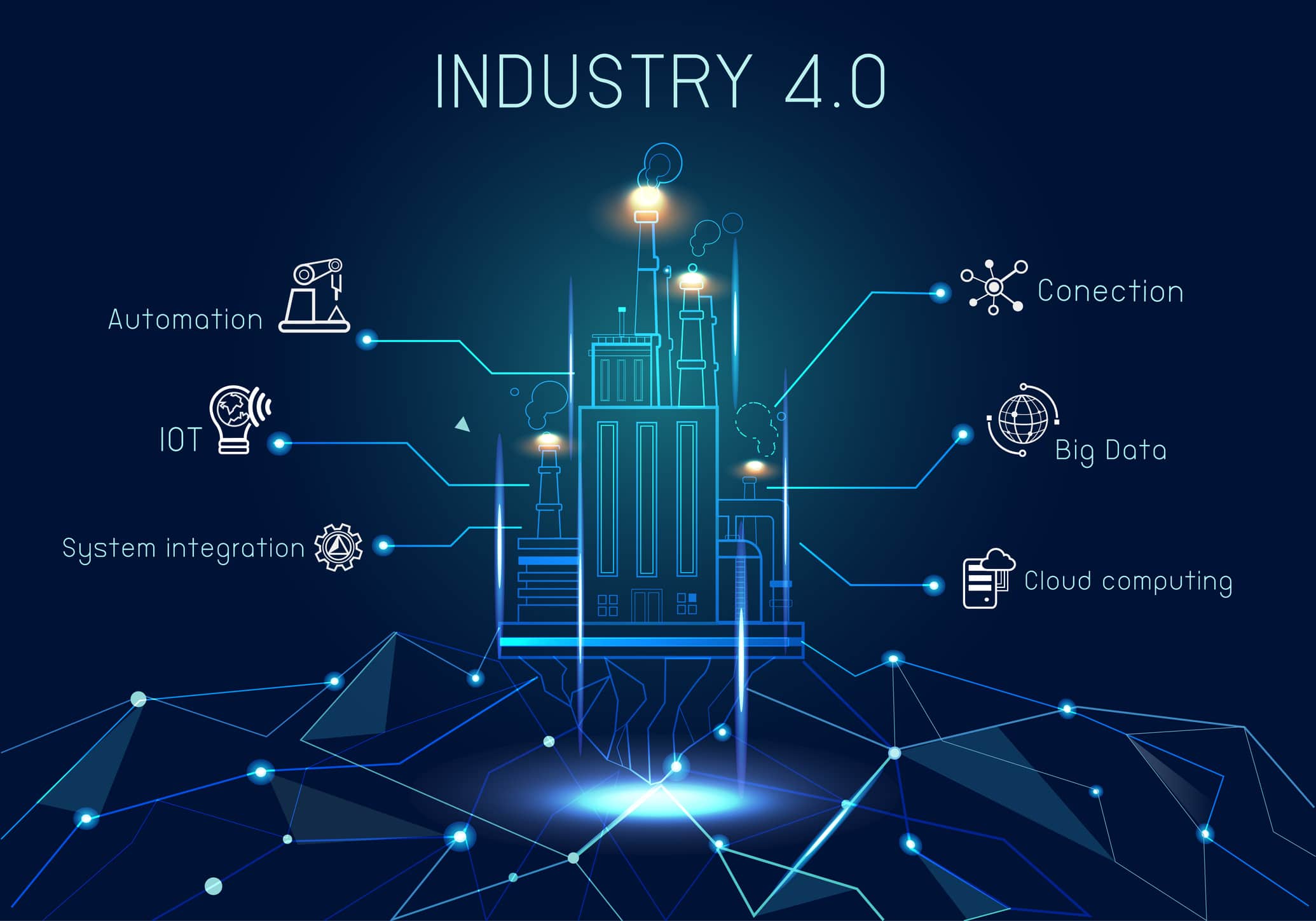
The term digital transformation has gathered a lot of steam recently. Ever since the pandemic, change has been a constant in the technology landscape, not that it was not before, but that now, many sectors have been forced to digitise or else face catastrophic drawbacks. Just like the digital world, the manufacturing world is a shifting tide of change in global, economic, and policy decisions.
In the manufacturing industry, digital transformation is not just about automating the assembly line or better analyzing existing data. It involves a change in mindset, approaches and new ways of problem-solving.
“I associate digital transformation with the integration of traditional manufacturing processes with Industry 4.0, the connecting of devices/machinery so that they can communicate and make decisions on their own. As with all forms of automation, an increase in efficiency has resulted, said Edwin Ngatia, Sales and Marketing Manager at Synkron International.
advertisement
Industry 4.0 is a trend that combines traditional manufacturing and industrial factories with digital. Also referred to as the fourth industrial revolution, the main purpose of Industry 4.0 is to automate production processes to the point where all processes are automated and controlled in real-time.
An example of that could be a machine with a sensor that interacts with another machine based on the data they receive, all happening without the intervention of another human. In the future, Industry 4.0 can blur the line of actual and virtual warehouses that can free manpower for more effective collaboration.
This is the playing field in which Synkron International runs the game, they are an engineering services company whose job is to improve the efficiency of the client’s automation and production process.
advertisement
Primarily working in the fast-moving consumer goods (FMCG) and pharmaceutical industries in East, Central and West Africa, The Synkron team comprises of specialist engineers trained in the mechatronic, mechanical and electrical engineering fields.
As digital technologies evolve all around us, manufacturers are increasingly coming to crossroads: to transform and develop or stick with the tried, tested, and true methods. These crossroads are just but a launching pad for Synkron, they have taken the bull that is digital transformation by the horns, and made it into a rodeo house.
With the understanding that data is a big part of the process. Sykron has reached a level where optimizing data usage in operations, allows them to utilise data more effectively. “What is not as obvious, however, is how much data is collected and how precious it can be if properly analysed. This data can be used to improve every facet of the manufacturing process from supply chain and enterprise to the shop floor and end users.” Explains Ngatia.
advertisement
A balanced combination of traditional manufacturing techniques and recent technologies such as the Internet of Things, cloud computing, data analytics, and machine learning is slowly becoming infused into the manufacturing processes. But, with the advent of all these technologies, dynamism is also key. Without dynamism, the core of technology is lost.
“The questions that we have historically asked our potential clients is ‘Do you have specialized packaging machinery? Does it require expertise not available in-house?’ If the answers were yes and no respectively, we would offer our services and if an agreement reached, deploy a team to site.” Avers Ngatia, portraying a fine example of dynamism.
The very essence of digitising an enterprise brings in collaboration tools and platforms that provide employees with easy access to information that they need with the flexibility to access it from anywhere and from any device. This would not only allow for lightning-fast response times in case of issues, but an overall ease of work.
“Teleservice is troubleshooting a machine remotely. This means that a specialist sitting in Synkron HQ can log into the client’s machinery and troubleshoot it.” adds Ngatia, bringing to light Synkron’s use of technology to meet customer demands.
He continues “Augmented Reality (AR) technology allows you to overlay images, videos and other digital information in a real-world physical environment. In our setup, the specialist based at Synkron HQ and your technician at the machine that requires an intervention are linked through a pair of AR glasses. The specialist is thus able to guide the technician on how to solve the problem. The glasses can also be used to carry out training.” This gives rise to how Synkron has gone beyond the hype of technology, and is using it now to harness data, developing strategies to keep the organisation on its toes. Noting with importance that the team behind facilitating Synkron’s are drawn from various equipment manufacturing powerhouses, namely Krones, KHS and Buhler.
As rubber meets the road for the fusing of technology into engineering and to an extension, manufacturing, it is wise to note that change is scalable. With a few small changes, manufacturers can improve their data, make better connections between systems. Ultimately making their business more digital, resulting in a better customer experience.
In the end, speed and information-rich, streamlined process optimisation efforts don’t just bring down costs but also are what both end customers and the many partners in the manufacturing ecosystem seek. “These technologies have additional benefits of time and cost savings for the client if you consider that travel and accommodation costs must be catered for (as well as visa costs if in a foreign country). The significant reduction in team deployment time has the added benefit of reducing machinery downtime and the associated costs,” mentions Ngatia.
Despite the initial shock and certain degree of confusion that pandemic has brought, manufacturers are now looking at their IT investments as a tool that will help them restore and adapt to the new reality faster. Company’s like Synkron have taken the old paradigm of factory and manufacturing and engineering, and thrown it out of the window. Now, they are the primary creators of shaping an entirely new paradigm, a paradigm where manufacturers are taking a closer look at their relationships with IT.
Synkron International have sponsored the CIO100 Symposium and Awards, slated for November 19th and 20th. Owing to the changes brought about by the pandemic, the event will unfold virtually.
The CIO100 Symposium and Awards will offer invaluable insights on the innovative tactics used by top tech people, and company’s, in today’s historically demanding environment. Plus, details of innovative projects that are positioning companies for current and longer-term success. CIO100 holds a space for the narrative of the industry, telling its stories through technologies.
Why CIO100? To acknowledge excellence in the adoption and use of IT within organisations – all of them, small, large or midi, appreciating the brilliant minds building products that responded to business needs and objectives. Also, patting these achievers on the back. This has over the last decade, catalysed innovation.
In its 11th year and still going strong, the CIO100 Awards fete 100 organisations that have shown outstanding results for leveraging technology to innovate ways of delivering business value, in a two-day summit.
The Awards recognise excellence in the adoption and use of ICT, awarding both the organisation and the Chief Information Officer (CIO), or an equivalent in the organisation. The winners of the CIO100 Awards are recognised at the CIO100 Symposium and Awards, a two-day high energy celebration of IT excellence, marked with networking opportunities and knowledge sharing that acknowledges the mark of enterprise excellence in the region.
Register for the CIO100 Symposium and Awards here.