advertisement
Manufacturing The Future
Manufacturing as was known in the past is rapidly evolving due to the new technologies that have become part of…
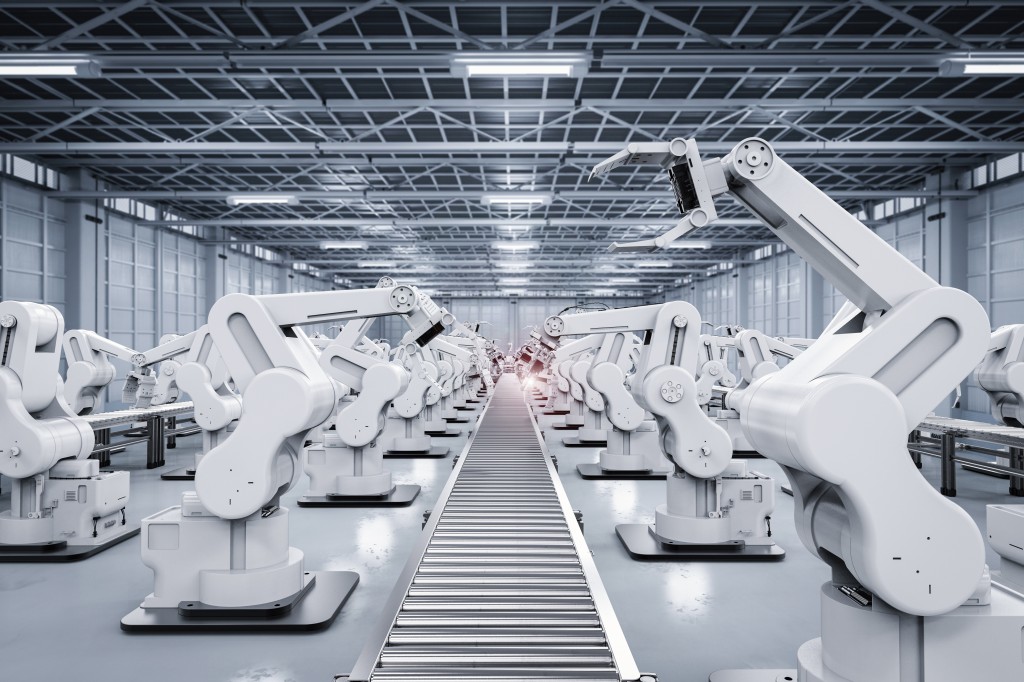
Manufacturing as was known in the past is rapidly evolving due to the new technologies that have become part of that space.
Artificial Intelligence, Advanced Robotics, and the Internet of Things, together with the Industrial Internet of Things are a few among others new technologies driving this change. Also known as ‘Industry 4.0’ technologies, they are poised to reshape the global manufacturing landscape, with important consequences for the traditional role of manufacturing.
In her keynote address during the #CIOIndustry40Forum, Dierdre Fryer, the Head of Solution Engineering at SYSPRO noted that the changing economics of production and distribution, along with shifts in consumer demand and the emergence of smart products, are pushing manufacturers to explore radically new ways of creating and capturing value.
advertisement
She said, “Manufacturing is no longer simply about making physical products. It is about making the future.”
Themed; Transforming the Manufacturing Value Chain, the inaugural virtual forum hosted the manufacturers within the East Africa region, who shared their digitisation journeys, in what experts noted as being akin to what the global manufacturing space is currently facing.
Intimamting on the dynamism of manufacturing today, Fryer added that by 2025, a new global consuming class will have emerged, and the majority of consumption will take place in developing economies that create a rich new market opportunity thus the need for manufactures to leverage 4.0 technologies to scale.
advertisement
Fryer, who was discussing the future of manufacturing, urged manufacturers to digitise in order to replace the manual and paper-based processes with standardised digital and automated processes, that seamlessly connect and orchestrate industry operations.

I4.0 technologies have however not been on the rise in East Africa as recent reports point out, hindering manufacturers from releasing truly innovative offerings of their own.
This lag has been characterized by the high cost of adopting such technologies and when the funds avail, then which technologies warrant this significant resource investment required to navigate digital transformation and embrace the promises of Industry 4.0 promises.
advertisement
As Fryer avered, some of the key technologies to look out for include, advanced robotics and automation, additive manufacturing and 3D printing, 5G technology, and the (Industrial) Internet of Things among others.
A PwC survey dated 2019 on the Internet of Things reported that manufacturers are optimistic about IoT with 93pc believing that its benefits exceed its risks, 68pc of which plan to increase their investment over the next two years.
“Manufacturers who haven’t implemented IoT are behind their competitors,” reads the report in part. “81pc of industrial manufacturers have applied IoT to increase operational efficiency and almost two-thirds plan to increase their IoT investment over the next few years.”
Rob Mesirow, leader of the PwC Connected Solutions/IoT practice notes that manufacturers should identify the most popular IoT use cases to better guide their own deployment plans. The main use cases are in logistics, supply chain, employee and customer experience, and predictive maintenance.
Fryer, however, warned that while implementing these technologies, especially IoT, cybersecurity concerns should be prioritized as attackers are always prying on vulnerable IoT devices for their malicious gains.