advertisement
How the Super Swedes developed the world’s strongest bolt – Bumax
With development and manufacturing in central Sweden’s historic steel belt, with heritage from the 1600s and home to several steel…
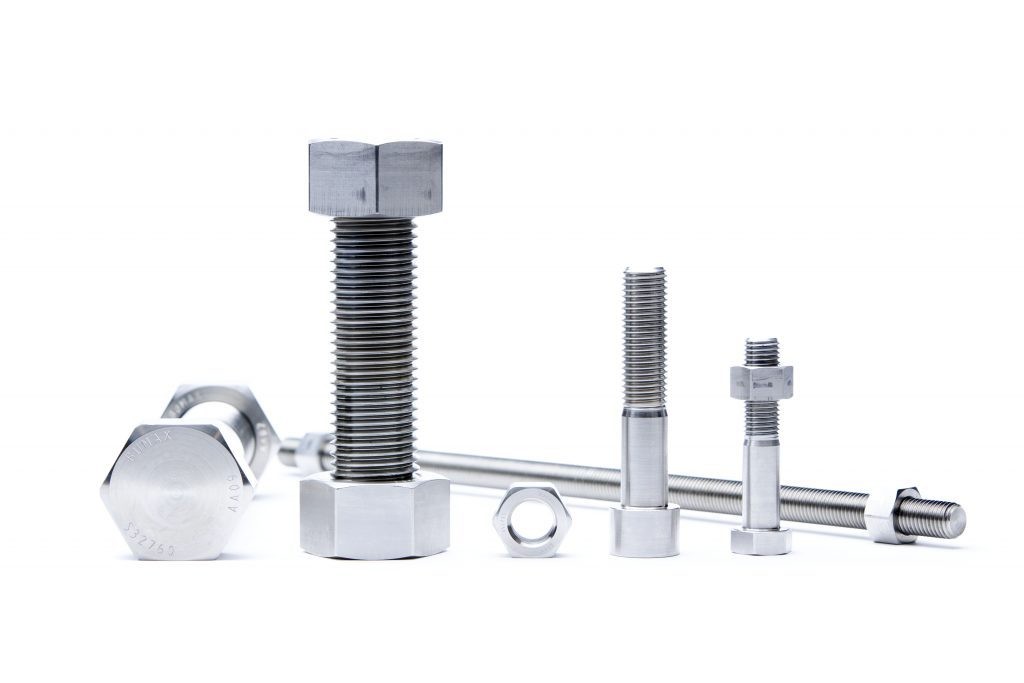
With development and manufacturing in central Sweden’s historic steel belt, with heritage from the 1600s and home to several steel making companies such as Sandvik and Outokumpu, premium stainless steel fastener manufacturer BUMAX produces what is now widely known as the strongest fastener in the world.
Far beyond standard, its super strong Bumax Ultra bolt has proven itself in various highly-demanding critical fastener applications around the world – providing optimal safety and reliability where standard fasteners are simply inadequate. BUMAX Ultra typically offers a yield strength of over 1,350 Megapascals (MPa), a unit of stress used to quantify material strength. Yield strength or yield stress is the material property defined as the stress at which a material begins to deform plastically.
So what does this mean? 1,350 MPa is three times the strength of standard stainless steel ‘class 70’ fasteners (450 MPa) and more than twice that of strong ‘class 80’ fasteners (600 MPa). The fact that BUMAX Ultra can handle more than double the load of a standard stainless steel fastener is a game changer for critical fastener applications by providing enhanced solutions that simply were not available a few years ago.
advertisement
Drawing on Nobel Prize winning technology
And how did they do it? BUMAX has been manufacturing premium stainless steel bolts since 1926. What their engineers and scientists don’t know about steel isn’t worth knowing. Often, BUMAX customizes fastener solutions for global clients with extremely demanding challenges.
The company capitalized on its own material technology knowledge and that of its premium stainless steel supplier, as well as its advanced manufacturing techniques, to develop the world’s strongest bolt.
advertisement
BUMAX Ultra ensures ultra-high strength and good corrosion resistance by drawing on Nobel Prize winning quasi-crystalline precipitate technology. Materials Science Professor Dan Shechtman won the 2011 Nobel Prize in Chemistry for his work with quasi-crystals, which has fundamentally altered how chemists conceive of solid matter.
The BUMAX technique uses strain hardening followed by precipitation hardening, which significantly increases the yield strength of the stainless steel by ensuring the crystal structure reinforces the material. The entire BUMAX Ultra range of fasteners are made at the BUMAX factory in Åshammar, a village of 550 inhabitants in central Sweden in which BUMAX is of course the largest employer.
The strongest bolt in the world – and it’s stainless
advertisement
Stainless steel fasteners are often selected for their corrosion resistance properties, however reduced strength has historically been an accepted compromise of using stainless steel rather than carbon steel. BUMAX Ultra has changed all that by providing ground-breaking solutions for highly demanding critical applications. It far exceeds carbon steel in terms of yield strength.
“BUMAX specializes in the development of high-strength stainless fastener solutions – to ensure superior corrosion resistance, while exceeding the mechanical properties offered by carbon steel, standard stainless products and many high alloy fasteners,” explained Örjan Persson, Business Development Director at BUMAX. “Our unique stainless steel fasteners such as BUMAX Ultra have revolutionized the fastener market by far exceeding carbon steel in terms of yield strength.”
Demanding applications – space, military, fueling and high pressure
Since its launch, the BUMAX Ultra range has proven that it is capable of exceeding yield strengths of over 1,350 in various applications, with good corrosion resistance and an operating range of between -50 and 400°C (-58 to 752°F).
Since the super strong Swedish fastener is designed for applications that require ultra-high strength combined with high ductility and fatigue resistance, applications include the most challenging imaginable – including security lock systems, aerospace systems, military applications, high pressure applications, fueling systems and semiconductor manufacturing equipment.
And it has met all expectations with excellent results. Installers of security lock systems value it for its excellent fatigue properties combined with strength, developers of aerospace systems appreciate its good fatigue, corrosion and strength properties as an alternative to titanium fasteners and manufacturers of high-pressure applications welcome its high strength.
Replacing carbon steel fasteners in critical applications
BUMAX Ultra fasteners are increasingly used to replace high-strength carbon steel fasteners in critical applications with extreme requirements on strength, ductility and fatigue resistance.
The very high strength-to-weight ratio in combination with the Ultra’s good formability and ductility also make it a cost-effective fastener alternative to other lightweight materials such as titanium.
All BUMAX Ultra fasteners are custom made to meet the requirements of each specific application and can be delivered with different mechanical properties.
“Ultra is an advanced engineering grade and we provide close technical support for customer projects in order to develop the optimal end solution,” added Örjan Persson, Business Development Director at BUMAX. “Even yield strength exceeding 1,350 MPa is possible with BUMAX Ultra, together with good corrosion resistance, formability and ductility.”
As a real-life example, a leading European lock and locking system manufacturer originally used a carbon steel screw for the critical latch screw. Following breakages that disabled the entire locking mechanism, the manufacturer tested various dimensions and grades without solving the problem.
The manufacturer then fatigue-tested BUMAX Ultra, which survived 500,000 strokes without a single breakage – compared with carbon steel screws that only lasted 10,000 strokes. Needless to say, BUMAX Ultra screws are now a critical lock component that helps ensure lock reliability.
Peter Karaszi and Richard Cutler are professional technical writers with decade long experience from covering manufacturing, materials science and new technologies.